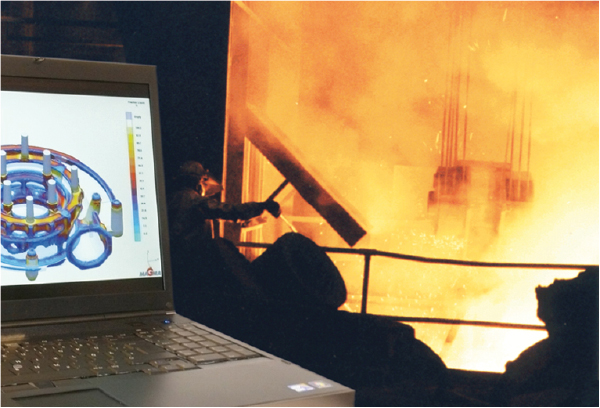
Christof Heisser, MAGMA Foundry Technologies, Inc., Schaumburg/IL ABD
Malzemelerin efektif olarak geri dönüşümü konusunda dökümhaneler “dünya şampiyonları” olarak ön plana çıkmaktadır. Döküm parçalarının % 90’ından fazlası yeniden ergitilmiş hurda metallerden üretilmektedir. Bu durum yalnızca metalle de sınırlı kalmamakta; döküm malzemeleri (kum) ve su da neredeyse hiç atık kalmayacak şekilde etkin bir şekilde tekrar tekrar kullanılmaktadır.
Buna rağmen, dökümhanelerdeki enerji ve malzeme giderleri, tüm giderlerin yaklaşık olarak % 40’ına karşılık gelmektedir. Bu oran personel giderlerine ayrılan miktar ile neredeyse aynıdır. Metallerin ergitilmesi ve katılaşması çok yüksek miktarda enerji gerektirmektedir. Fiziksel kurallar, bir tonluk bir döküm ürün için ortalama 2,000 kWh enerji girişi gerekliliğini ortaya koymaktadır. Bu rakamlar, Alman döküm endüstrisinin yıllık 11 milyar kWh’luk enerji tükettiği anlamına gelmektedir. Bu enerjinin % 50’sinden fazlası yalnızca son döküm için değil, metalin boşluklara yönlendirilmesi konusunda önemi büyük olan yolluk ve besleyici sistemleri için kullanılmaktadır. Yolluk ve besleyici sistemleri aynı zamanda katılaşma prosesi esnasında metalin ergimiş ve katı hali arasındaki hacim farkını ortadan kaldırma konusunda döküm için malzeme sağlamakta ve çekilme hatalarını ortadan kaldırmaktadır.
Bu noktada döküm proses simülasyonunun zaruri katkı sağladığı kanısı kaçınılmaz bir gerçek; Simülasyon, dökümhane mühendisinin metal dökülmeye başlamadan önce fiziksel ve teknolojik bir optimumda yolluk ve besleyici sistemi tasarlamasına olanak sağlamaktadır. Bu olanak ilk olarak gerekli malzeme miktarının minimize edilmesi, ikinci olarak ise ergitme prosesinde kullanılan enerjinin azaltılması ile iki şekilde enerji kazancı ortaya koymaktadır.
Simülasyonun enerji verimliliği ve bununla bağlantılı CO2 emisyonu azaltılması ile ilgili diğer önemli katkıları yüksek kapasiteli üretimlerde proses ve çevrim sürelerinin azaltılması sonucu sağlanmaktadır. Bu, sürekli döküm kalıplarının, gerekli ısıtma prosesi ve sıcaklık dağılımının optimize edilmesi ve bunun yanında maksimum parça sayısı ile model diziliminin ortaya konulması için kullanılmaktadır. Üretim prosesinin tamamı açısından bakıldığında simülasyon, döküm malzemesi miktarının azaltılması, kalıptan çıkarma koşullarının geliştirilmesi, temizleme ve yeniden işleme uygulamalarının elimine edilmesi konularında yardımcı olduğu için aynı zamanda enerji tüketimini de azaltmaktadır. Son üretim aşamasından önce gerçekleştirilen deneme ve hata çalışmaları ile önemli düzeyde dolaylı enerji kazançları sağlanmaktadır.
Bu nedenlerden dolayı döküm proses simülasyonu kullanımı ile birlikte bir dökümhanedeki enerji ve hammadde verimliliğinin önemli seviyelerde geliştirilebileceği ifade edilebilir. İlerleyen kısımlarda dökümhanelerden yer alan örnekler, mevcut CO2 tartışmalarında ortaya çıkan sorunlara simülasyonun ne şekilde çözüm bulabileceğini açıklayacaktır.
Giriş
Bir ton dökme demir üretimi için ortalama olarak 1,000 kWh’lık elektrik gücü ve 100 kg kok gereklidir. Bu rakamlar, bir ton son döküm ürün için 1,500 – 2,000 kg CO2 emisyonu anlamına gelmektedir [1]. Bir ton son ürün için ortalama 5,600 kWh enerji girişi gerekir, bu da ton başına yaklaşık olarak 2,500 kg CO2 emisyonuna denk düşmektedir [2]. Almanya’da yıllık 5,9 milyon ton metal ergitilip dökülmektedir (4,8 milyon ton çelik ve dökme demir, 1,1 milyon ton demir dışı malzemeler [3]). Bu ortalama rakamlar göz önünde bulundurulduğunda (Bir ton son döküm ürünü için 2,000 kWh, Almanya’daki 1 kWh elektrik gücü için 563 g CO2 [4]) Alman dökümhanelerinin yıllık enerji tüketiminin yaklaşık olarak 11 milyar kWh ve CO2 emisyonunun yine yaklaşık olarak 6.5 milyon ton olduğu belirtilebilir. Bu rakamlara bakıldığında enerji tasarruflu “yeşil” dökümhanelerin iklim düzenlemesine katkısının çok olacağı aşikârdır.
Bu yüzden döküm endüstrisi uzun zamandır, yalnızca ekonomik sebeplerden ötürü, enerji kazancı sağlayacak döküm proseslerinin kullanımı ve geliştirilmesi üzerine odaklanmış durumdadır. Dökümhanelerde enerji tüketimi, üretim giderlerinin büyük bir kısmını oluşturmaktadır ve dolayısıyla kar marjları ve rekabet gücü açısından çok önemli etkisi mevcuttur. Enerji kullanımının azaltılmasına yönelik kampanyaların temel odak noktaları, genellikle enerji tüketimi yüksek proseslerin optimizasyonu konusunda olmaktadır. Örneğin; ergitme prosesi ve dökümhane ekipmanlarının çalıştırılmasında verimliliği daha yüksek olan daha etkili fırınlar, izolasyon kapasitesi daha yüksek fırın astarları, enerji geri kazanımının kullanılması ya da basınçlı hava dağılımının optimize edilmesi ve benzeri birçok konu mevcut araştırma programlarının konusu dahilindedir.
Döküm proses simülasyonu ile daha az enerji ve hammadde girdisi
Döküm proses simülasyonu, bir dökümhanenin enerji verimliliğinin yükseltilmesinde çok önemli katkı sağlayabilmektedir. Gerekli hammadde miktarının ve bununla bağlantılı olarak bu malzemelerin prosesi için gerekli enerji tüketiminin azaltılması konularını çeşitli yönlerden desteklemektedir. Döküm üretiminde kullanılan enerjinin çok büyük bir oranı, yeniden ergitme ve yanma esnasında kaybedilir. Yeniden ergitilmiş malzeme miktarının azaltılması ve son döküm ürün miktarının toplam dökülen ağırlığa oranının (döküm verimi) artması durumunda önemli ölçüde enerji miktarı kazanılabilir. Döküm Teknolojileri Enstitüsü (Düsseldorf, Almanya), yapmış olduğu hesaplamalar sonucunda döküm veriminde % 60’dan % 70’e meydana gelecek bir artışın endüksiyon fırını kullanarak yılda 2,000 ton döküm üreten bir dökümhane için yıllık 300,000 kWh elektrik gücü kazanmasına neden olacağını belirtmiştir [1]. Enerji tüketimi, ilave olarak tüm proses zinciri içerisinde de azaltılabilir (Tablo 1 ve Şekil 12). Yalnızca tüm “enerji noktalarının” eksiksiz olarak optimizasyonu, CO2 emisyonlarının tasarruf edilecek şekilde azalmasına neden olabilir ve dökümhanelere maliyet ve rekabet açısından çeşitli avantajlar sağlar.
Tablo 1: Dökümhanelerde yer alan çeşitli proses aşamalarında dökme demir ve çelik için spesifik ortalama enerji tüketimi. Döküm proses simülasyonundan önemli ölçüde etkilenen alanlar kırmızı ile gösterilmiştir ([1] modifiye edilmiş).
Kalıba analitik bakış
Döküm proses simülasyonunun, enerji ve maliyet azaltılması için bir araç olabileceği fikri ilk kez Almanya, Aachen’ da ortaya çıktı. Bu yaklaşımın değeri, 1980’li yılların başında Alman Araştırma Konsorsiyumu tarafından çoktan fark edilmişti ve üretim proseslerindeki enerji ve hammadde kazançlarının iyileştirilmesi için temel ilkeleri RWTH Aachen’ın özel bir araştırma alanı çerçevesinde desteklendi [5].
1980’lerin sonunda döküm proses simülasyonunun dökümhanelere ulaşması ile birlikte ilk defa “Kara Kutu” kalıp içerisinin görsel olarak gözlemlenmesi ve belirlenen verilere göre proses koşullarının ve yolluk tasarımlarının optimize edilmesi mümkün hale geldi. Döküm proses simülasyonunun öncelikli hedefi, daha yüksek kaliteli döküm parçaları elde edebilmek için ekonomik, uygun maliyetli döküm proseslerinin geliştirilmesidir. Bu hedef, hammadde kullanımında enerji ve maliyet tasarrufunun arttırılması amacının gerçekleştirilmesi ile alakalıdır. Döküm proses simülasyonunun, döküm ve proses geliştirme ve prototip aşamalarında sistematik olarak kullanımı ilave maliyet tasarrufu sağlamaktadır. Bunlara ek olarak, sürekli döküm kalıplarındaki sıcaklık dağılımlarının geliştirilmesi ve ısıl işlem gibi başarılı prosesler aracılığıyla verimliliğin arttırılması sayesinde de enerji tasarrufu gerçekleştirilebilir. Simülasyon, aynı zamanda ürün ve proses geliştirme sürelerinin azaltılması, iletişimin geliştirilmesi (işletme içi ve müşteriler ile), bunun yanında çalışanların eğitimleri ve ortaklaşa bilgilerinin gizlilik içermeden dokümantasyonunun sağlanması gibi çeşitli avantajları ile maddi anlamda da birçok faydalar sağlamaktadır.
Son 30 yıl içerisinde dökümhanelerdeki döküm proses simülasyon araçları, zamanla sadece hata algılama ve yolluk geliştirme aracı niteliğinden, tüm verimin geliştirilebileceği ve güvenilir proseslerin sağlanacağı kabul edilebilir bir yöntem haline dönüştü. Simülasyonun bu rolü kuşkusuz dökümhane uzmanlarının, simülasyon sonuçları ardından ortaya koymuş oldukları güven üzerine dayanmaktadır. Bu nedenle proseslerin tahmini olarak tanımlanması, döküm teknolojisinin ilk varsayımlarını onaylamak için sadece bir kez hesaplanmamakta, aynı zamanda üretim prosesinin stabilitesi üzerindeki önemli proses parametrelerinin etkilerinin belirlenmesi amacı ile, parametre ve hassasiyet çalışmalarını yürüttüğü için bir “görsel test dökümhanesi” olarak kullanılmaktadır. Bu olanak bir dökümhanedeki önemli parametrelerin enerji ve malzeme verimine etkisinin incelenmesi ve anlaşılması için temeli oluşturmaktadır. Yazının devamında verilecek olan örnekler bu bağlantıları açıklayacaktır.
Maliyeti düşüren dökümlerin hazırlanması
Ağırlık azaltma, otomotiv ve ekipman üretim endüstrilerindeki en önemli teknoloji olarak ön plana çıkmaktadır. Bir araçta meydana gelecek 100 kg’lık bir ağırlık azalması, yakıt tüketiminin 0.41/100 km’ de 0,2 azalmasına eş değerdir. Toplamda 250,000 km mesafe kaydetmiş bir aracın yaşam döngüsü süresince 1,000 litreye kadar yakıt ya da 2,3 ton CO2 tasarrufu edilebilir. Bunun yanında ekipman üreticilerinin düşük ağırlık koşulları altında düşünmesi gerekir. Örneğin, büyük rüzgar enerjisi türbininin planlanan rüzgar enerjisi kaportalarının artan ağırlığı, kritik bir fizibilite ve başarı faktörü haline gelmiştir.
Modern simülasyon araçlarının kullanımı ile döküm malzemelerinin ve bu malzemelerin üretim proseslerinin tüm potansiyelini açığa çıkarmak mümkündür. Günümüzde simülasyon araçları proses parametrelerinin döküm kalitesi üzerindeki etkilerini hatasız şekilde tahmin etme olanağına sahiptir. Bu araçlar üretim prosesinin ilk aşamalarında ağırlığın azaltılması için kullanılabilir. Simülasyon programlarından elde edilen bilgiler tasarımcının yalnızca dökülebilir ve ağırlık optimizasyonu sağlanmış tasarımları bulmasını değil aynı zamanda dökümhane mühendislerinin güvenilir ve uygun maliyetli üretim oluşturmasını da destekler.
İlk olarak tasarımcılar yük gerekliliklerini karşılayacak bir model oluşturur. Potansiyel bir tedarikçinin işin içine dahil olması durumunda döküm prosesi ile ilgili bilgi birikimi çoğu zaman tasarım aşamasına da dahil edilir. Süreç içerisindeki bu noktada tasarım aşaması çoğunlukla bitmiştir ve döküm prosesinin gerektireceği herhangi bir değişiklik birçok iş yüküne ve tasarımcı ile tedarikçi arasında gerçekleşecek maliyetli iletişim döngüsüne neden olur. Üretim maliyetlerinin %80’inin dökümün tasarım aşamasında belirlendiği ifade edilmiştir. Özellikle düşük ağırlık gereksinimleri konusunda özel ilgi gereken parçalarda döküm proses simülasyonunun olabildiğince erken olaya dahil edilmesi çok önemli faydalar sağlamaktadır (Şekil 1). Simülasyon kullanıldığı ve tasarımcı ile tedarikçi simülasyon sonuçları üzerine inceleme yaptığı zaman, döküm prosesi için problem ve dolayısıyla kalite sorunu yaratabilecek tasarım özellikleri çok geç olmadan fark edilebilmektedir. Bu durum özellikle döküm prosesi, ısıl işlem ve akabinde gerçekleştirilen işleme uygulamalarının, son parçanın özelliklerini belirlediği çok aşamalı üretim proseslerinde daha önemli bir hal almaktadır.
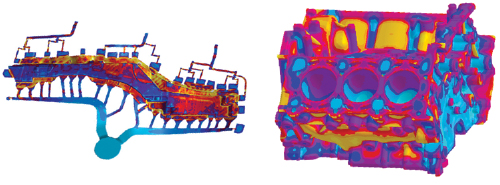
Şekil 1: Dökümlerdeki düşük ağırlıklı tasarım, tüm döküm malzemeleri ile elde edilebilir (sol: AlSi9Mn alaşımından yapılmış Audi D4 Bağlantısı [6], sağ: Sıkıştırılmış grafitli dökme demirden yapılmış, ağırlık optimizasyonlu Audi V6 motor bloğu [7].)