Giriş
Hassas döküm, kalıp malzemesi olarak mum, kil, plastik gibi çeşitli malzemelerin kullanıldığı ve harcanabilir kalıp kullanılan endüstriyel bir prosestir. Binlerce yıl öncesinde Mısırlılar, Yunanlılar ve Romalıların mücevher yapımında kullandığı bu yöntem, kayıp mum prosesi olarak da adlandırılabilir. Halen ince ve keskin detaylı kalıptan çıkamayacak parçaların dökümündeki en etkili yöntemdir. Procast tüm metalurjik mekanizmaların karmaşıklığını hesaba katarak, dökümhane mühendislerine ürünlerini geliştirme aşamaları için etkili bir araç sunar.
Process Karakteristiği
Bu proses diğer döküm yöntemleriyle üretimi mümkün olmayan karmaşıklıktaki parçaların üretimine olanak tanır. İşlem sonrasında az miktarda yüzey bitirme gerekebilir. Ulaşılan hassas boyutsal toleranslardan dolayı gerekecek işleme ise sadece minör seviyede olacaktır. Ağırlık olarak birkaç gramdan 20 kg’a kadar parçalar dökülebilirken %0.5 boyut toleransı yakalamak her zaman mümkündür. Daha küçük boyutlu dökümlerde ise
%0.15 gibi toleranslar yakalanabilir. En küçük et kalınlığı 0.5 mm-1 mm olan parçalar dökülebilir. Hassas döküm dökülebilir her metalle yapılabilmesine rağmen demir, alüminyum, nikel, kobalt, titan, bakır ve magnezyum alaşımları en çok kullanılanlardır.
Hassas döküm bazı yönlerden işleme, dövme ve diğer döküm yöntemleriyle karşılaştırılabilir fakat bu işlemlerin yararlı yönlerini tek bir proseste birleştiren tek şekillendirme yöntemidir. Hassas döküm türbin bıçakları, jet motoru parçaları gibi çeşitli metal ve yüksek performanslı alaşımlardan yapılmış parçaların üretimini sağlarken aynı zamanda yüksek hassasiyet, tekrar edilebilirlik gibi faydaları da beraberinde sunar.
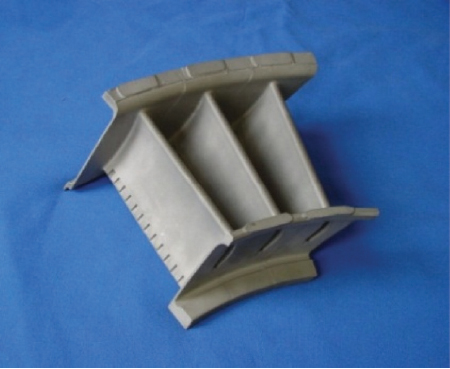
Figur 1- Hassas dökümle üretilmiş turbin bıçakları. (alaşım IN 718) Yaklaşık boyutlar 150mm * 180mm* 1.5 mm (CSIR izniyle)
Proses Aşamaları
Birinci kritik aşama mum şablonun yapım aşamasıdır. Harcanabilir şablon yapımı için genellikle alüminyumdan yapılmış kalıplar gereklidir.
Birkaç mum şablon harcanabilir bir şablon ağacı oluşturması için yolluk üzerine bağlanır. Tüm ağaç ateşe dayanıklı bir balçığın içine daldırılır ve dış yüzeyde balçıktan bir kaplama oluşur. Kurumaya bırakıldıktan sonra istenen kalınlığa gelinceye kadar işlem tekrarlanır. Daha sonra tüm şablon ağacı mumun erimesi için fırına koyulur ve yavaş yavaş küçük bir açıklık belirir. Geriye üretilmek istenen parçanın her detayını yakalamış ve içi erimiş metalle doldurulacak olan içi boş bir hacim ortaya çıkar. Katılaşma sürecini etkilemesi için yalıtım malzemesi kullanımı sık kullanılan bir yöntemdir. Erimiş metal katılaştıktan sonra kalıp kırılır ve döküm ortaya çıkar. Dikkatli bir kontrolden sonra döküm temizlenir ve sonraki işlemlere tabi tutulur.
Kalıp için kullanılan malzeme gypsum plaster gibi bir yapıştırıcı ile toz silika gibi ateşe dayanıklı bir malzemenin karışımıdır. Sonrasında uygulanacak bitirme işlemine göre silimanit ve etil silikat gibi kaplamalarda kullanılabilir.
Figür 2 – Hassas döküm için kabuki üretiminin aşamaları
Figür 3 – PROCAST ile kabuki modelleme. Çoklu seramik katmanlar ileri düzey mesh fonksiyonları ile hassas olarak modellenebilir (Microcast’ın izniyle ).
Doldurma işleminin hemen öncesinde kalıp içinde kalmış mum artıklarının erimesi için kalıp 1000°C seviyelerine kadar ısıtılır. Bu aynı zamanda yapıştırıcı malzemesinde sertleşmesini sağlar.
Erimiş metali önceden ısıtılmış kalıbın içine dökmek metalin seramik kabukla teması esnasında oluşabilecek erken katılaşmanın da önüne geçer. Bu akış yolunun kesit alanına göre uzun olduğu durumlarda daha önemlidir. Erimiş metali doldurmak işlemi yerçekimi, basınç ve vakum kullanılarak da yapılabilir.
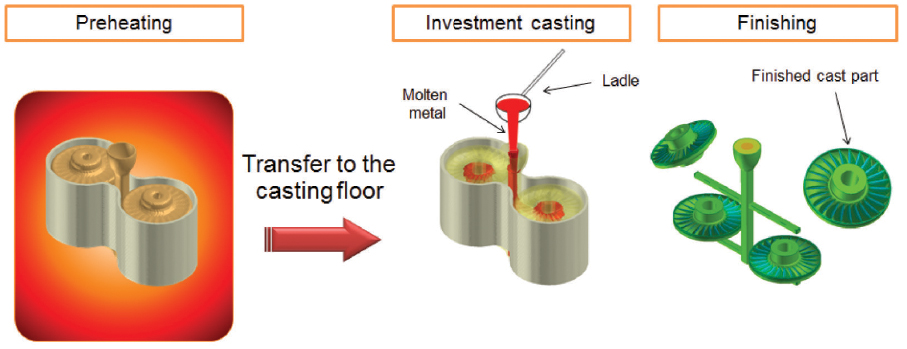
Figür 4 – Ön ısıtmadan bitirmeye kadar hassas döküm aşamaları.

Figür 5 – PROCAST Proses sonrası ile görüntülenmiş parçacık takibi görüntüsü.(Microcast izniyle).
Krom, nikel, kobalt, molibden gibi bazı malzemeler oksijene karşı yüksek çekim gösterir. Ortaya çıkan oksitlenme reaksiyonu ürünün dayanımını düşürmekle kalmayıp, bundan daha önemlisi parçanın içinde kalan oksit parçacıklarından dolayı potansiyel performansa ve mekanik özelliklere zarar vermektedir. Bu olay yüksek performanslı dökümlerin, oksitlenmeyi asgariye indirerek vakum altında yapılmasının ana sebebidir. Böyle malzemelerin kullanıldığı türbin endüstrisi ve uzay endüstrisi buna örnek oluşturur.
Procast’ın son geliştirmeleri dolum şablonu, oksit, renkli akış yolu, birleşim, malzeme yaşı, parçacık takibi gibi parametreleri ileri düzeyde görselleştirmeyi sağlar. Örnekle, akışkan önü takibi belirleyicisi oksitlerin ve katkıların son pozisyonlarını aynı zamanda akış birleşim noktalarını temiz bir şekilde görselleştirebilir.
Procast ile Döküm Simülasyonu
Döküm simülasyonu temel olarak 3 aşamadan oluşur.
Ön Proses: CAD verisini alma, geometriyi benzetim amaçlarına göre yerleştirme, ağ yapıyı oluşturma.

Figür 6 – Parça kesitindeki sıcaklık dağılımı. Boşluk oluşumu kırmızı çemberle belirtilmiştir, (Microcast izniyle).
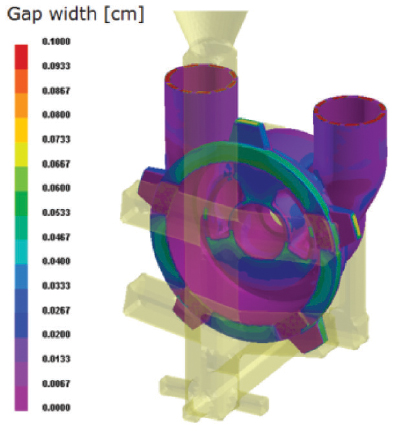
Figür 7 – Dökümdeki boşluk genişlikleri (Microcast izniyle).
Model Hazırlama: Malzeme özelliklerini tanımlama
Gerçek prosese göre başlangıç ve sınır şartlarının tanımlanması ve istenen fiziksel sonuca uygun çözücünün seçilmesi
Proses Sonrası: Analiz sonuçlarının görüntülenmesi
Modellemeden türetilmiş öngörüler benzetim programının kalıptaki ısı kaybını modelleyebilme kabiliyetiyle yakından alakalıdır.
Hassas dökümdeki kalıbın soğuması öncelikli olarak ışıma temelli olduğundan görünüş faktörü hesaplamalarında tüm bölgelerdeki çok yönlü radyasyon etkisi hesaplar dâhilinde olmalıdır.
Döküm parçası ısıyı temas ettiği seramik kalıba dağıtarak katılaşmaktadır. Aynı zamanda temasın verimliliği katılaşmanın sonucu olan çekme ve boşluk oluşumundan etkilenerek geometriye ve zamana bağlı olarak değişmektedir. Procast tüm prosesi döküm mühendisinin kullanımı için doğru olarak modelleyebilir.
Bu noktadan sonra hassas döküm simülasyonu ile ilgili bazı resimler gösterilmiştir. Analizler tasarımı modifiye etmek, parça dayanımını iyileştirmek amacıyla Procast ile yapılmıştır.
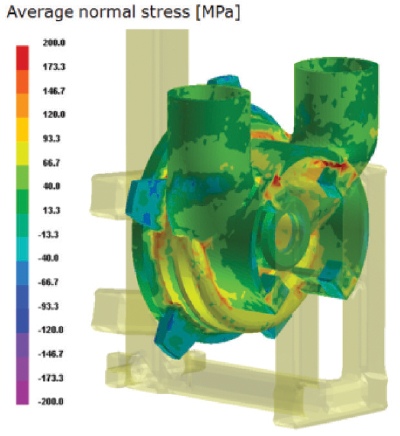
Figür 8 – Averaj normal stres, çekme altındaki bölgelerin gösterimi (Microcast izniyle).
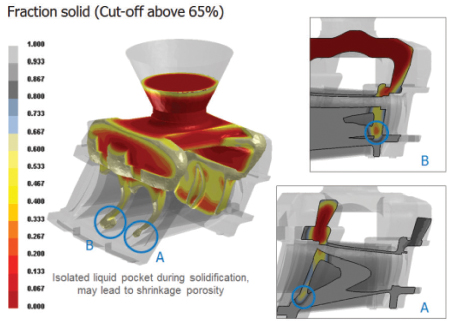
Figür 9 – Katı oranının bağzı görüntüleri. Sıvı boşlukları belirtilmiştir (EMA izniyle).

Figür 10 – Çekme porozitesi (EMA izniyle).
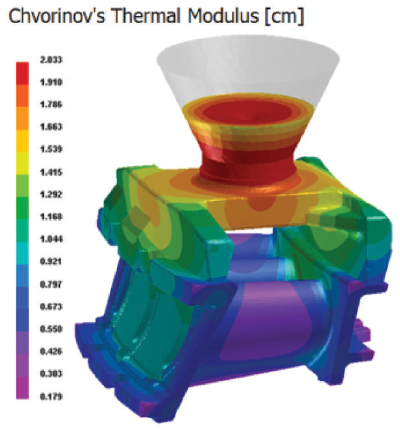
Figür 11 – Chvorinov termal modulu (EMA izniyle).

Şekil 12
CC / DS / SX Prosesleri
Soğuma aşamasını kontrol altına alarak yönlendirilmiş kristal yapı elde etmek mümkündür. Küçük değişimlere bağlı olarak eşit katılaşma (CC), yönlendirilmiş katılaşma (DS) ya da tekli kristal oluşabilir. Özellikle uzay endüstrisinde Procast ileri düzey bir algoritma olan 3 boyutlu hücresel sonlu elemanlar yöntemi ile kendisini ispatlamıştır.
Sonuç
Tüm döküm prosesini ESI grubun yeni “visual environment” arayüzü ile görselleştirmek, akışla ilgili problemleri, katılaşmayı, parça kaymalarını ve mikro yapıyı tasarımcılar ve mühendisler için görülebilir kılmaktadır.
Bilgisayar benzetimleri tasarım ve üretim arasındaki boşluğu kolaylıkla doldurur. Procast fikirleri test etme olanağı ve bunların sonuçlarını görselleştirerek değerlendirme imkânı sağlarken masrafları asgari de tutup zaman kaybını azaltır ve pahalı olan malzemeden tasarruf sağlar.